ROUND BARS
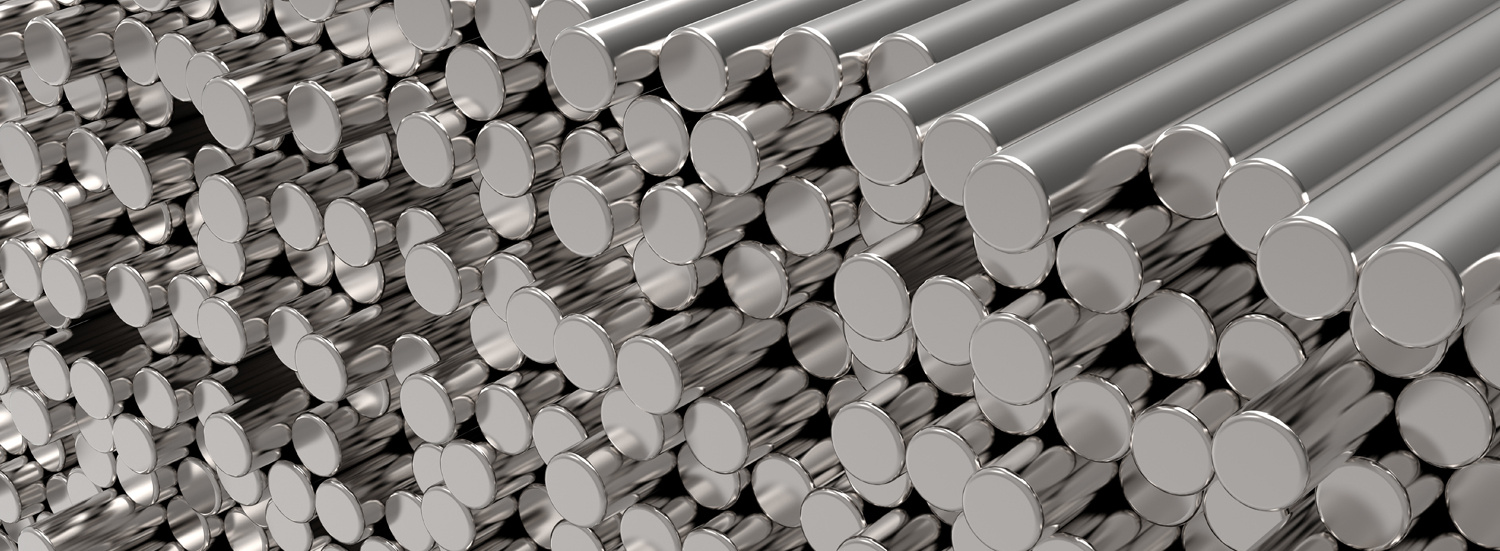
Size range | 5mm – 110mm (3/16″ – 4 1/3″) |
Forged Size range | 150mm – 400mm (5/90″ – 16″) |
Supply conditions | |
Length | Up to 6.5 meters |
Tolerances | h8, h9, h10, h11, h12, k12, k13, A-484, EN-10060, DIN-1013 etc. |
Surface finish | RA upto 0.2 mm (8.7 RMS) |
Straightness | Up to 0.5 mm per meter TIR |
Grit polish | K240,K320 or as per customer’s requirement |
Heat treatment | Soft annealing, solution annealing, oil & water quenching, tempering & normalizing |
Bars end finish | Chamfered ends, 300, 450 & 600 plain ends without burrs or sharp edges |
Specifications | As per EN, DIN, JIS, ASTM, BS, ASME, GHOST, AISI/Nace MRO175 |
Cold drawn, centreless ground, peeled & polished, rough peeled or smooth turned bar | |
Grade Confirmation through PMI testing with Handheld Spectrometer. | |
Free from radioactive elements, mercury & lead contamination |
HEX BARS
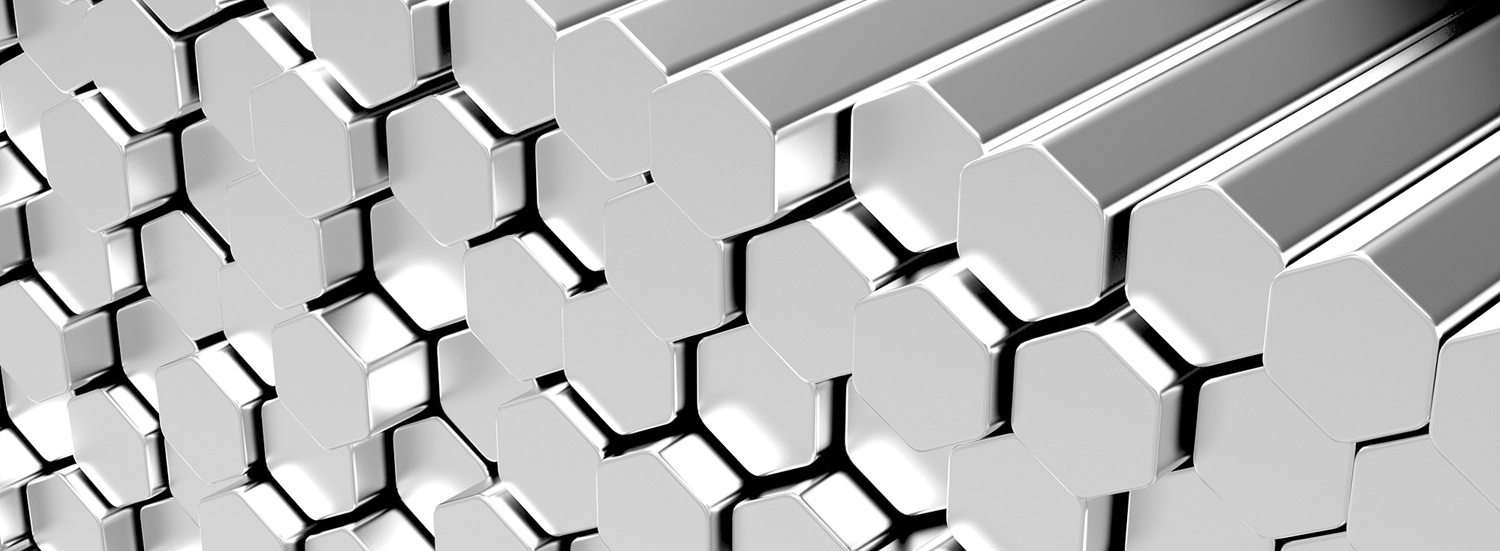
Size range | 15mm – 55 mm ( 3/5″ – 2 1/6″) |
Supply conditions | |
Length | Up to 6 meters |
Tolerances | h11, k12, k13 |
Grit polish | As per customer’s request |
Heat treatment | Solution annealed, oil & water quenched / tempered, soft annealing |
Bars end finish | Chamfered ends, plain ends without burrs or sharp edges |
Specifications | As per EN, DIN, JIS, ASTM, BS, ASME, AISI, etc. |
Grade confirmation through PMI testing with handheld spectrometer. | |
Free from radioactive elements, mercury & lead contamination. |
SQUARE BARS
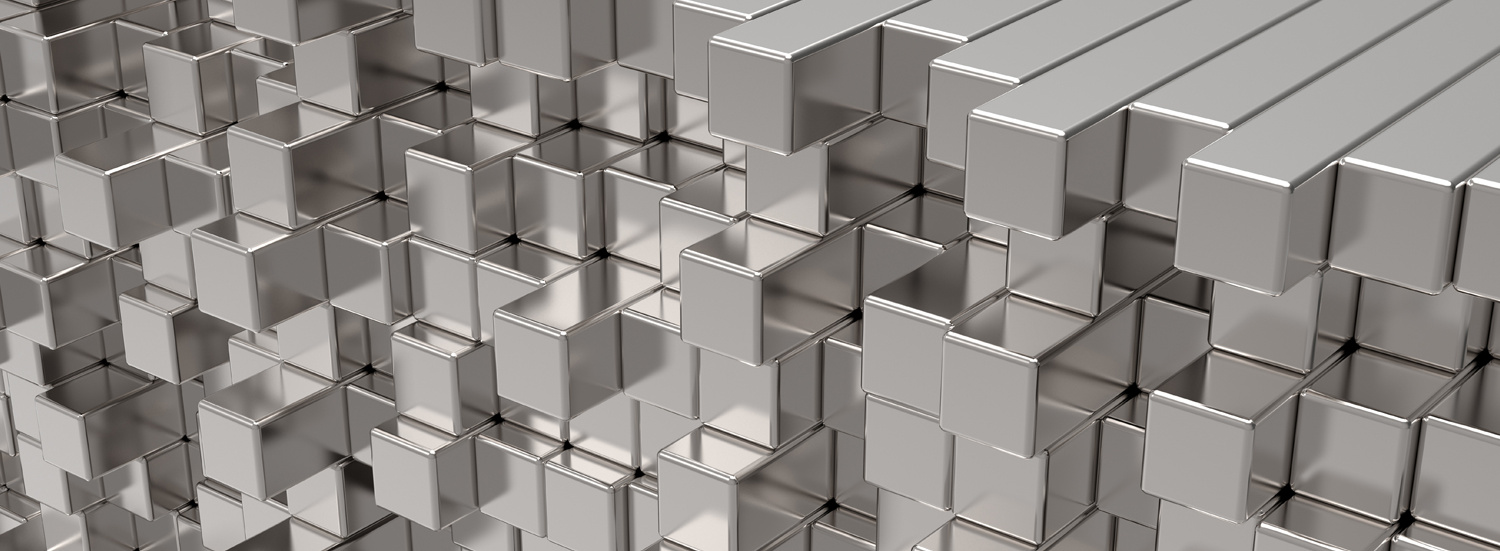
Size range | 12.70 mm – 58 mm (1/2″ to 2-2/7″) |
Supply conditions | |
Length | Up to 6 meters |
Tolerances | h11, k12, k13 |
Grit polish | As per customer’s request |
Heat treatment | Cold drawn, solution annealed, oil & water quenched / tempered |
Bars end finish | Chamfered ends, plain ends without burrs or sharp edges |
Specifications | As per EN, DIN, JIS, ASTM, BS, ASME, AISI, etc. |
Grade confirmation through PMI testing with handheld spectrometer. | |
Free from radioactive elements, mercury & lead contamination. |
Specified Size, in (MM) | Permissible Variation from | Out of Round or Out of Square in (MM) | |
Specified Size in (MM) | |||
Over | Under | ||
3/16 to 7/16 (8.00 to 11.00), incl | 0.006 (0.15) | 0.006 (0.15) | 0.009 (0.23) |
3/16 to 7/16 (8.00 to 11.00), incl | 0.007 (0.18) | 0.007 (0.18) | 0.010 (0.26) |
Over 5/8 to 7/8 (15.50 to 22.00), incl | 0.008 (0.20) | 0.008 (0.20) | 0.012 (0.30) |
Over 7/8 to 1 (22.00 to 25.00), incl | 0.009 (0.23) | 0.009 (0.23) | 0.013 (0.34) |
Over 1 to 1-1/8 (25.00 to 28.00), incl | 0.010 (0.25) | 0.010 (0.25) | 0.015 (0.38) |
Over 1-1/8 to 1-1/4 (28.00 to 31.50). incl | 0.011 (0.28) | 0.011 (0.28) | 0.016 (0.42) |
Over 1-1/4 to 1-3/8 (31.50 to 34.50), incl | 0.012 (0.30) | 0.012 (0.30) | 0.018 (0.46) |
Over 1-3/8 to 1-1/2 (34.50 to 38.00), incl | 0.014 (0.35) | 0.014 (0.35) | 0-021 (0.53) |
Over 1-1/2 to 2 (38.00 to 50.00), incl | 1/64 (0.40) | 1/64 (0.40) | 0.23 (0.60) |
Over 2 to 2-1/2 (50.00 to 63.00), incl | 1/32 (0.80) | 0 | 0.23 (0.60) |
Over 2-1/2 to 3-1/2 (63.00 to 90.00), incl | 3/64 (1.20) | 0 | 0.035 (0.90) |
Over 3-1/2 to 4-1/2 (90.00 tom 115.00), incl | 1/16 (1.60) | 0 | 0.048 (1.20) |
Over 4-1/2 to 5-1/2 (115.00 to 140.00), incl | 5/64 (2.00) | 0 | 0.058 (1.50) |
Over 5-1/2 to 6-1/2 (140.00 to 165.00), incl | 1/8 (3.00) | 0 | 0.70 (1.80) |
Over 6-1/2 to 8 (165.00 to 200.00), incl | 5/32 (4.00) | 0 | 0.85 (2.20) |
Over 8 to 12 (200.00 to 300.00), incl | 3/18 (4.80) | 0 | 3/32 (2.40) |
Over 12 to 15 (300.00 to 400.00), incl | 7/32 (5.50) | 0 | 7/64 (2.80) |
Over 15 to 25 (400.00 to 625.00), incl | 1/4 (6.50) | 0 | 1/8 (3.20) |
DIN Tolerance |
||||||||
Size Range | h6 | h7 | h8 | h9 | h11 | h12 | h13 | K12/K13 |
Over 1MM to 3MM | =0/-0.006 | =0/-0.01 | =0/-0.014 | =0/-0.025 | =0/-0.06 | =0/-0.1 | -0.14 | – |
Over 3MM to 6 MM | =0/-0.008 | =0/-0.012 | =0/-0.018 | =0/-0.03 | =0/-0.075 | -0.12 | -0.18 | – |
Over 6MM to 10MM | =0/-0.009 | =0/-0.015 | =0/-0.022 | =0/-0.036 | =0/-0.09 | -0.15 | -0.22 | – |
Over 10MM to 18MM | =0/-0.011 | =0/-0.018 | =0/-0.027 | =0/-0.043 | =0/-0.11 | -0.18 | -0.27 | – |
Over 18MM to 30MM | =0/-0.013 | =0/-0.021 | =0/-0.033 | =0/-0.052 | =0/-0.13 | -0.21 | -0.33 | =0.1/0.15 |
Over 30MM to 50 MM | =0/-0.016 | =0/-0.025 | =0/-0.039 | =0/-0.062 | =0/-0.16 | -0.25 | -0.39 | =0.15/0.2 |
Over 50MM to 80MM | =0/-0.019 | =0/-0.03 | =0/-0.046 | =0/-0.074 | =0/-0.19 | -0.3 | -0.46 | =0.2/0.25 |
Over 80MM to 120MM | =0/-0.022 | =0/-0.035 | =0/-0.054 | =0/-0.087 | =0/-0.22 | -0.35 | -0.54 | =0.25/0.3 |
Hardness Conversion Chart |
||||
Brinell Hardness HB | Vickers Hardness HV | Rockwell Hardness HRC | Rockwell Hardness HRB | Tensile Strength ksi |
321 | 339 | 34 | 108 | 158 |
311 | 328 | 33 | 108 | 154 |
302 | 319 | 32 | 107 | 150 |
293 | 309 | 31 | 106 | 146 |
285 | 301 | 30 | 105 | 142 |
277 | 292 | 29 | 104 | 138 |
269 | 284 | 28 | 104 | 135 |
262 | 276 | 27 | 103 | 131 |
255 | 269 | 25 | 102 | 25 |
248 | 261 | 24 | 101 | 121 |
241 | 253 | 23 | 100 | 119 |
235 | 247 | 22 | 99 | 117 |
229 | 241 | 21 | 98 | 113 |
223 | 234 | – | 97 | 110 |
217 | 228 | – | 96 | 107 |
212 | 222 | – | 95 | 102 |
207 | 218 | – | 95 | 100 |
202 | 212 | – | 94 | 98 |
197 | 207 | – | 93 | 96 |
192 | 202 | – | 92 | 94 |
187 | 196 | – | 91 | 90 |
183 | 192 | – | 90 | 89 |
179 | 188 | – | 89 | 87 |
174 | 182 | – | 88 | 84 |
170 | 178 | – | 87 | 82 |
166 | 175 | – | 86 | 80 |
163 | 171 | – | 85 | 78 |
159 | 167 | – | 84 | 77 |
156 | 163 | – | 83 | 76 |
153 | 160 | – | 82 | 75 |
149 | 156 | – | 81 | 74 |
146 | 153 | – | 80 | 72 |
143 | 150 | – | 79 | 71 |
140 | 147 | – | 78 | 70 |
137 | 143 | – | 76 | 67 |
134 | 140 | – | 75 | 66 |
131 | 137 | – | 74 | 65 |
128 | 134 | – | 73 | 64 |
126 | 132 | – | 72 | 63 |
124 | 129 | – | 71 | 62 |
121 | 127 | – | 70 | 60 |
118 | 124 | – | 69 | 59 |
116 | 122 | – | 68 | 58 |
114 | 119 | – | 67 | 57 |
111 | 117 | – | – | – |
AISI ASTM | EN DIN | C % Max | Mn % Max | Si % Max | S % Max | P % Max | Cr % Max | Ni % Max | Mo % Max | Others % |
201 | – | 0.15 | 5.5-7.5 | 1 | 0.03 | 0.06 | 16-18 | 3.5-5.5 | – | N 0.25 max |
202 | – | 0.15 | 7.5-10 | 1 | 0.03 | 0.06 | 17.00-19.00 | 4.00-6.00 | – | – |
302 | 1.431 | 0.15 | 2 | 1 | 0.03 | 0.045 | 17.00-19.00 | 8.00-10.00 | – | – |
302HQ | 1.4567 | 0.03 | 2 | 1 | 0.03 | 0.045 | 17.00-19.00 | 9.00-10.00 | – | Cu : 3.00-4.00 |
303 | 1.4305 | 0.15 | 2 | 1 | 0.15 Min | 0.2 | 17.00-1900 | 8.00-10.00 | – | Cu : 1% max |
303EHS | – | 0.15 | 2 | 1 | 0.30-0.33 | 0.2 | 17.00-19.00 | 8.00-10.00 | – | Cu : 1% max |
304 | 1.4301 | 0.08 | 2 | 1 | 0.03 | 0.045 | 18.00-20.00 | 8.00-11.00 | – | – |
304HC | – | 0.05 | 2 | 1 | 0.03 | 0.045 | 18.00-20.00 | 8.50-9.50 | – | Cu : 2.00-2.50 |
304L | 1.4306 | 0.03 | 2 | 1 | 0.03 | 0.045 | 18.00-20.00 | 8.00-12.00 | – | – |
308LER | 1.4331 | 0.02 | 1.5-2.0 | 0.5 | 0.02 | 0.025 | 19.00-21.00 | 9.50-11.00 | – | – |
309LER | 1.4332 | 0.03 | 1.5-2.0 | 0.5 | 0.015 | 0.02 | 23.00-25.00 | 12.00-14.00 | – | – |
310 | 1.4841 | 0.25 | 2 | 1.5 | 0.03 | 0.045 | 24.00-26.00 | 19.00-22.00 | – | – |
310 | 1.4841 | 0.25 | 2 | 1.5 | 0.03 | 0.045 | 24.00-26.00 | 19.00-22.00 | – | – |
310S | 1.4842 | 0.08 | 2 | 1.5 | 0.03 | 0.045 | 24.00-26.00 | 19.00-22.00 | – | – |
316 | 1.4401 | 0.08 | 2 | 1 | 0.03 | 0.045 | 16.00-18.00 | 10.00-14.00 | 2.00-3.00 | – |
316L | 1.4404 | 0.03 | 2 | 1 | 0.03 | 0.045 | 16.00-18.00 | 10.00-14.00 | 2.00-3.00 | – |
316LER | 1.443 | 0.02 | 1.5-2.0 | 0.5 | 0.02 | 0.02 | 18.00-20..00 | 12.00-14.00 | 2.00-2.75 | – |
316Ti | 0.08 | 2 | 1 | 0.03 | 0.045 | 16.00-18.00 | 10.00-14.00 | 2.00-3.00 | Ti : Min (5xC%) | |
317LN | 1.4438 | 0.03 | 2 | 1 | 0.03 | 0.045 | 18.00-20.00 | 11.00-15.00 | 3.00-4.00 | N : 0.10-0.22 |
321 | 1.4541 | 0.08 | 2 | 1 | 0.03 | 0.045 | 17.00-19.00 | 9.00-12.00 | – | Ti : Min (5xC%) |
410 | 1.4006 | 0.15 | 1 | 1 | 0.03 | 0.04 | 11.50-13.50 | – | – | – |
416 | 1.4005 | 0.15 | 1.25 | 1 | 0.15 Min | 0.06 | 12.00-14.00 | – | – | – |
416XM | – | 0.15 | 1.25 | 1 | 030-0.33 | 0.06 | 12.00-14.00 | – | – | – |
420 | 1.4021 | 0.15 Min | 1 | 1 | 0.03 | 0.04 | 12.00-14.00 | – | – | – |
430 | 1.4016 | 0.12 | 1 | 1 | 0.03 | 0.04 | 16.00-18.00 | – | – | – |
430L | – | 0.03 | 1 | 1 | 0.03 | 0.04 | 16.00-18.00 | – | – | – |
430F | 1.4104 | 0.12 | 1.25 | 1 | 0.15 Min | 0.06 | 16.00-18.00 | – | – | – |
431 | 1.4057 | 0.2 | 1 | 1 | 0.03 | 0.04 | 15.00-17.00 | 1.25-2.50 | – | – |
ASTM A 276 |
Standard specification for stainless and heat resisting steel bright bars and shapes. This specification covers hot finished or cold finished bars except bars for re-forging and hot rolled or extruded shapes, such as angles, tees and channels in the more commonly used type of stainless steel, excluding the free matching types of general corrosion resistance and high temperatures services. |
ASTM A 314 |
Standard specification for stainless and heat resisting and bars for |
forgings. The specification covers stainless and heat resisting steel billets |
and bars intended only for forgings. |
ASTM A 476 |
Standard specification for stainless and heat-resisting steel bars and |
shapes for used in boilers and other pressure vessels. |
The specification covers hot and cold finished bars of stainless and heat |
resisting steel, including rounds, squares and hexagons and hot-rolled or |
extruded shapes such a angles, tees and channels for use in boiler and |
pressure vessels construction. It is also related to the ASME boiler and |
ressure vessel code SA-279 section II. |
ASTM A 484 |
Standard specification general requirements for stainless and heat- |
resisting bars, billets and forgings. |
This specification covers general requirements which shall apply to |
stainless and heat resisting wrought steel bars, shapes forgings and |
billets or other semi-finished material (except wire) for forging. Pertinent |
details contained in this specification are tolerances for size, width, |
thickness, length and straightness of bars materials. |
ASTM Tolerance |
Stainless and heating resisting bars are produced in various conditions |
and surface finished. It is important that conditions be associated with the |
appropriate finish because each finish is not applicable to every |
condition. |
Conditions and Surface Finish |
Stainless and heating resisting bars are produced in various conditions |
and surface finished. It is important that conditions be associated with the |
appropriate finish because each finish is not applicable to every condition. |